What Can Service Do for You?
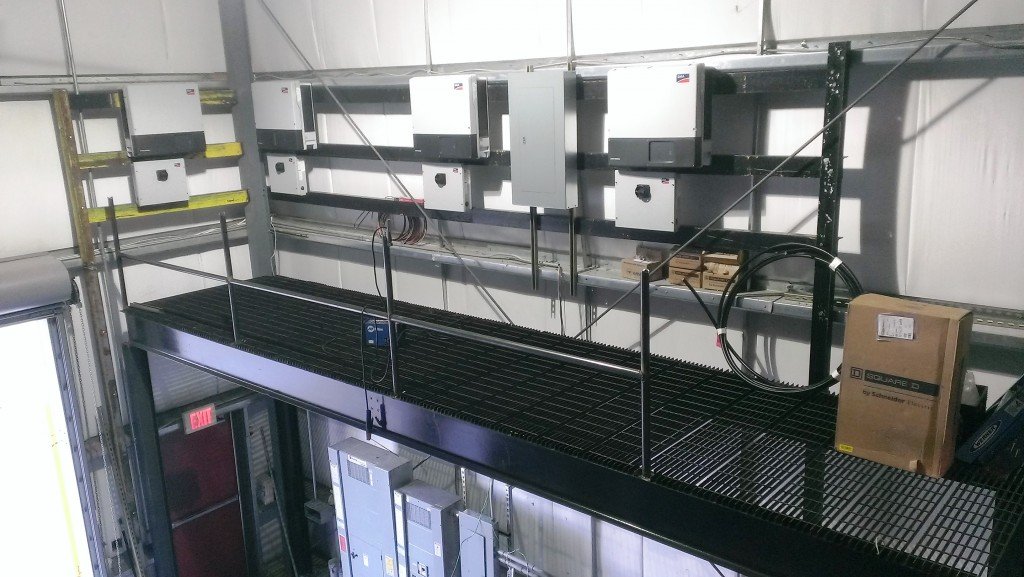
The endless lists of components and options have been considered, system designs and mock-ups created and everything ordered—modules, racking, inverters, and the list goes on and on. But what happens when something goes wrong or didn’t come out as planned? While most companies might believe that once a deal is done there is nothing left they can do for you, we think otherwise.
Case in point
When Ralph Pasquarella first designed the solar system to offset electrical costs for his business, RMP Warehouse Refrigeration, he submitted his plans to Connecticut Light & Power and was approved to participate in their Power Purchase Agreement program.
His system would have used 288 ET Solar 300W modules with eight Sunny Boy 8000TL-US inverters and one Sunny Boy 7000TL-US, all run through a power balancer to accommodate the three phase power that’s onsite. After further review by CL&P, they determined the original plans didn’t satisfy their interconnection requirements and the power balancer wasn’t UL listed and wouldn’t be approved for use.
The solution
Having modules and racking already installed and strung for the previous inverter design created two possible yet unfortunate options: installing a relay at each inverter with a phase-loss monitor or changing the string sizes for an alternate inverter design. In either solution, labor costs associated with the new design would exceedingly lengthen the systems payback period.
Pasquarella took a different route and contacted Greg Smith from SMA’S Solar Academy. Given the installed modules and string sizes, Smith determined the current configuration would work as-is with three Sunny Tripower 20000TL-US and one Sunny Tripower 15000TL-US inverter. Between the system’s initial design and the need to re-design, SMA’s Sunny Tripower inverters arrived in North America and became the solution for Pasquarella’s problems.
Trouble connecting
Once the Sunny Tripowers were installed, Pasquarella was optimistic about having the system commissioned and generating power. Even with the best of intentions, a second round of set-backs prevented any power from being generated and Pasquarella contacted the SMA Service Line for help.
SMA’s John Barton and Pasquarella quickly discovered the problem and Barton shipped connection units to Connecticut to get the system ready for commissioning in short order, despite working late into the night on Christmas Eve.
“We encountered a range of problems getting this system from start to finish,” said Pasquarella. “What made the difference between success or failure was the SMA’s dedication to see it through to the end. They had confidence from day one that a good solution would be found and they kept their word. Without SMA, I’d have been left in the dark.”
Green Light
After all was said and done, Pasquarella’s system received final approval from CL&P and was commissioned on the next available sunny day. Considering the work it took getting the system from initial mock-ups to final inspection, waiting for a pause in the winter storms was the least of their worries. In the months following, the only struggle has been finding breaks in this year’s exceedingly tough winter to clear snow off the modules!
Feel free to contribute!